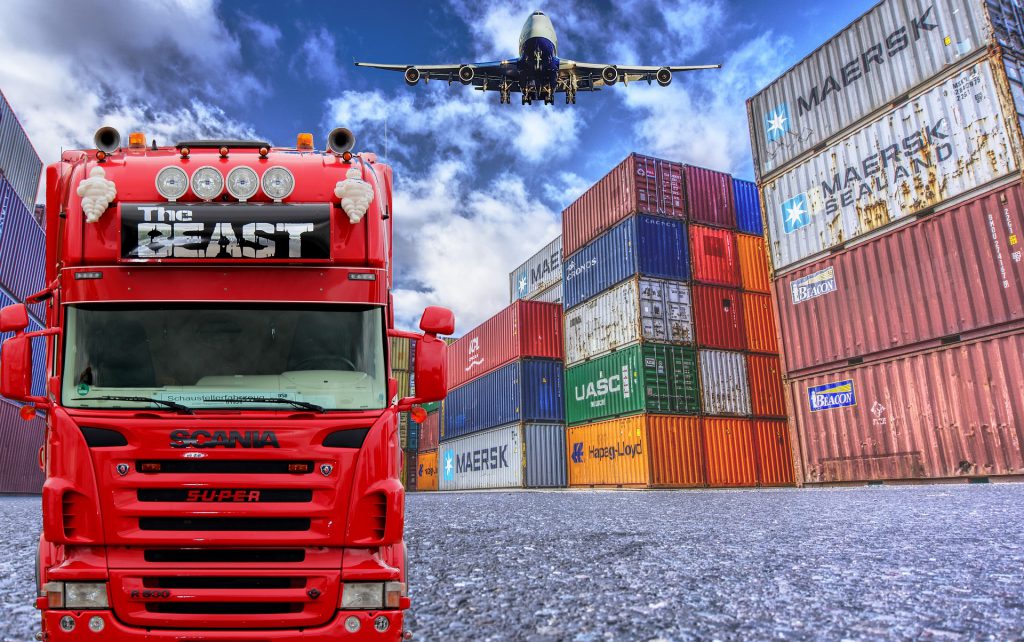
Supply Chain Resiliency
What Is It and Why Is It Important?
Supply Chain Resiliency, that’s a term that has garnered quite a bit of attention over the past few years. Surprisingly, not many companies have given much thought to the topic so in this post I thought we could briefly highlight what it is, why it’s important and some of the considerations that go into planning.
First we must define the term. Many people view a supply chain as something very limited. They might view it as a product being produced in a factory which then gets delivered to a distributor to sell the product, to the product ending up in it’s final home with a consumer when in fact a supply chain is much more complex. Supply chain begins with the raw material. Take a tantalum capacitor as an example, the tantalum has to be mined, processed, and sent to the capacitor manufacturer who is also bringing in raw materials from steel wire, plastics, and aluminum yet this is only one minor component in a perhaps extensive PCB assembly. This same type of supply chain applies to every component and sub component on the board. So when we talk about the resiliency of a supply chain, in a nutshell, it is the ability for an organization’s supply chain to continue to function when faced with foreseen and unforeseen stressors. As with almost everything else in life and business, to accomplish this the devil is in the details.
How do you identify those stressors or events or scenarios?
Once they are identified, how do you work with them or around them to keep your organization functioning properly. Who should be responsible for identifying these risks?
Most of these answers are quite dependent on the size and scope of the organization. For organizations with a global footprint like ours, the number of potential pitfalls and obstacles grows exponentially. In our organization, our management team reports in on a daily basis to discuss what challenges or possible challenges may lay ahead. For those subscribing as we do to the latest iteration of ISO 9001:2015 risk management is vital. These data points come from daily inputs from global news sources, customer conversations, foreign exchange forecasting by global financial institutions, the list goes on. A myriad of variables also exist in raw material costs, government regulations, and other natural impediments that can occur such as storms, natural disasters, civil unrest, or in the case of 2020, a global pandemic.
As a subscriber to the phrase proper prior planning prevents poor performance, considerable time and effort is spent in our organization thinking up worst case scenarios and how they might impact our supply chain, because if we cannot deliver, our customers suffer. This effort does not come without cost. In regards to purchasing and supply chain in recent years, it has been very easy to be penny-wise and pound foolish. I have seen companies on numerous occasions just hit the search box, click, and purchase without giving the needed attention to quality and repeat-ability of that part. In our case, we have done our best to have redundant manufacturing in different countries or regions. An expensive proposition for us, but a saving grace for our customers who found out last year and now this year that everything in the supply chain is not always sunshine and rainbows. This was also compounded by the imposition over the past few years of added import tariffs on products manufactured most notably in China and for some products in Europe and Canada among others. Our ability to produce in one of our less challenged facilities enabled us to keep our products flowing when most of our competitors were faced with large cost increases and higher regulatory burdens. It is also important to keep in mind that while these geopolitical issues play out and impact manufacturing efficiency, the economic factors continue to change. Rising material costs and declining (or increasing) currency values directly impact the cost of goods and usually not for the better.
So what to do? Conventional wisdom used to be that costs were always going to decline, you should place as small an order as possible because surely the next order will come faster and be cheaper. Those days are gone. When we work with our customers, we try to establish a risk profile on the part internally to help recommend optimum order sizes to ensure our customers have what they need when they need it and with the quality they expect. Sometimes this is a yearly blanket with monthly releases, other times it may be an order every 90 days. Much of that depends on what we see as potential impacts to its production and delivery. Approximately 70% of companies have had some disruption to their supply chain in the past 12 months based on our observations. Almost every potential customer we have spoken with has at a minimum seen a lengthening of lead times or a reduction in their time to market on new products (assuming they had a plan for doing this while working remotely). Very few had any type of resilience or predictive supply chain planning that they were relying on. Thankfully our system has worked quite well and although we operate in the same world all of our customers do, our customers did not see any real impact in what we provided to them during this latest global challenge.
If you are interested in how we might be able to boost your supply chain resiliency, please contact us for more information.