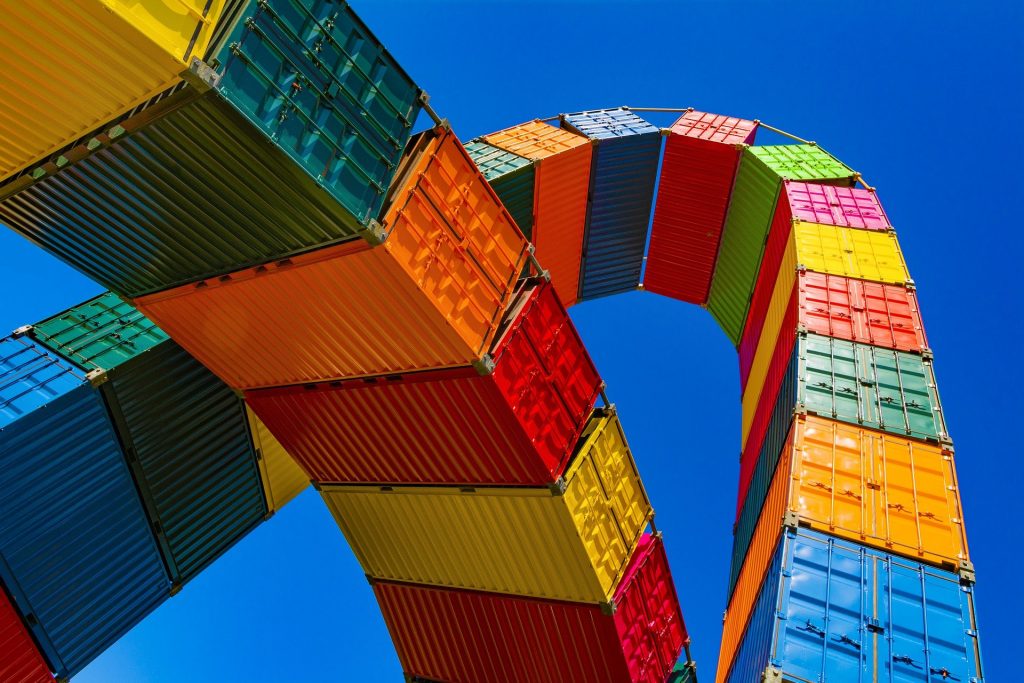
The Global Supply Chain
What’s Going On?
The current global supply chain is in a state of turmoil. We’ll take a look at the multiple factors that have contributed to this and how to move forward to avoid this in the future. Some of this supply chain disruption stems from logistics companies who are dealing with labor, ship, and container shortages while manufacturers and suppliers are dealing with parts and materials shortages. With all these shortages upending the front and middle of the global supply chain, the end consumer is left wondering when their product will be delivered.
Supply chain disruption is defined as a breakdown of the multifaceted process of an end to end supply of goods. A supply chain starts with the raw materials and ends with the final product that an end consumer buys off-the-shelf. Some companies control that entire process while others operate in a portion of that supply chain before they hand off responsibility to someone else.
There are many things that can disrupt a supply chain. In 2020 and 2021 alone, we have seen a record number of ships lose their containerized loads in heavy seas, winter storms that shut down the southern United States for a week, a container ship block the Suez Canal, a semiconductor, plastics, and lumber shortage, and to top it all off the COVID-19 pandemic that catapulted all the regular supply issues into a major crisis.
If you can manufacture your products on time, the bigger issue becomes the logistics of getting the product to its final destination. Shipping companies are not offering new service contracts allowing companies to lock in rates on their containers as they have done in the past. Instead, the rates quoted are now all spot rates and these have skyrocketed sometimes up to 20x where it was in 2019. Something as simple as human error and high winds causing a ship to wedge itself in the Suez Canal can have catastrophic consequences as the Suez is one of the main channels for container ships to quickly make their way from the Far East to the Mediterannean and Northern Europe. When you block that main waterway, ships are stuck waiting behind it or they have to find alternate routes around the blockage that can add several extra weeks to the voyage. The US West Coast is having major delays. Once you’ve gotten your product to the U.S., the next issue is getting the containers off the ship quickly and onto the rail system or getting them picked up by a trucking company. With the current labor, truck, and chassis shortages, the cost of trucking products from one city to another is multiples of what it used to be.
Many companies have become accustomed to regularly dealing with supply chain disruptions but 2020 and 2021 have led to the incredible upheaval that makes it appear as though the wheels have come off the bus and we’re spiraling out of control.
How Did This Happen?
To determine all the variables that led us to this point, we need to first look at some basic manufacturing processes. Just in Time (JIT) planning was a practice that became widely adopted after Toyota’s pioneering of the concept in 1938. JIT allows OEM’s and other manufacturers to only receive as much product as they need when they need it instead of holding onto a backlog of thousands of components in inventory until the production runs are completed. This concept has always had an inherent peril. It works perfectly when you have no stressors or plan for stressors that can be accommodated. Most companies never adopted a truly robust JIT system because of the sheer cost of maintaining inventory for their customers. Most used some variation that has left them vulnerable to the current logistics climate. The result is that many of these companies who didn’t fully stock up and plan for disruption are left short and unable to deliver products to their customers due to the shortages caused by the COVID-19 pandemic. Currently, we’re seeing a knee-jerk reaction by these suppliers that has resulted in companies overcompensating by trying to get more products on hand than is actually needed because they don’t want to be left short again. This in turn has created a massive bottleneck in production across a wide range of industries and materials which creates supply shortages that put inflationary pressure on prices. This, coupled with a huge increase in money supply, creates a self-perpetuating spiral of disruption and increasing prices.
How Can I Protect Myself and My Business?
With all the unknowns, it’s important to have a manufacturing partner that’s keeping your best interests in mind as you navigate the unknowns in today’s tumultuous supply chain. Supply chain resilience has been a recent buzz phrase and those companies who have a full view of their supply chain are able to anticipate and counter disruptions as they happen. Paying attention to warning signs and being proactive is how you will survive the next year.
Keep up to date with current events, know how those events could affect your business, and counter them to the best of your ability to stay ahead. Make sure that you are planning your production process properly. If you know how much product you produce in a given year, make sure you have your components in production well in advance of your need so you can easily mitigate the disruptions that are always going to be a threat to your process.
As always, Knight Electronics will be happy to be your manufacturing partner if you need someone to guide you and your business through difficult disruptions and decisions.