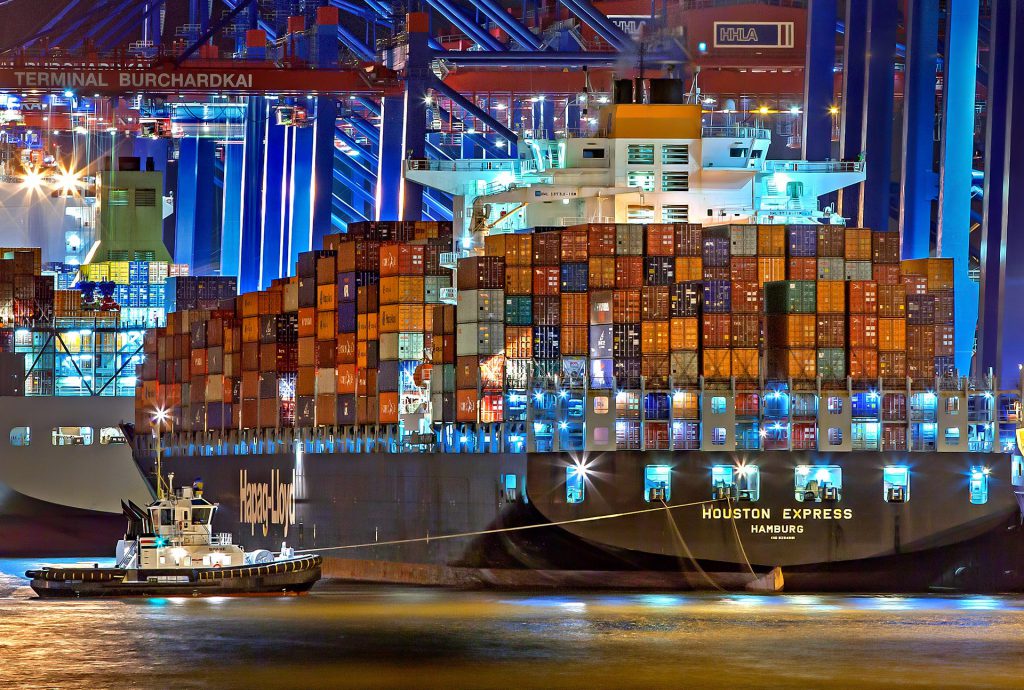
Marine Casualties
What’s The Deal?
If you have been paying close attention to global news sources lately, there would seem to be an unusual number of ships coming from the far East that have suffered marine casualties as of late. These merchant vessels are an integral part of the supply chain for nearly every major industry in the U.S. so when things go wrong, it can rapidly cause a major disruption to multiple organizations.
There have been four notable events over the past 60 days, the first is the loss of approximately 2,000 containers overboard (out of a capacity of 14,400) off of the vessel M/V ONE Apus in a storm Northwest of Hawaii on November 30, 2020. There are additional losses from crushed containers that remained aboard resulting in a significant financial loss on this cargo. When all is said and done it is estimated the cargo loss numbers will likely be north of $250 Million USD. The vessel was diverted back to Kobe, Japan and as of this writing in late January, they have only unloaded approximately 300 containers. Cargo that was undamaged is not likely to get to their consignees for 9 months or more. Many consignees still don’t know if their cargo was lost or not so the consignees are still unable file an insurance claim.
This event was followed by another casualty aboard the M/V Ever Liberal on December 31, 2020 in a storm off the coast of Japan with the loss of 36 containers overboard and another 21 40′ containers falling to the deck (hope it wasn’t fragile). The ship continued on to the US West Coast but the effects of losing those few containers leaves several organizations with wrinkles in their supply chains.
Not to be outdone, a 3rd major casualty occurred aboard the M/V Maersk Essen on January 16, 2021 losing approximately 750 containers over board out of a capacity of 13,200 during a storm in the mid pacific on the way from Xiamen, China to LA/Long Beach. Because of the extreme duress the port of Los Angeles and Long Beach is currently under with ships waiting 7-10 days to get alongside and discharge, the ship elected to divert to Lazaro Cardenas, Mexico, (Mexico’s largest container port), to assess damage and figure out how to get the remaining cargo to their respective consignees and effect any repairs that may be needed to the vessel. This will also likely take months to resolve.
This was followed on Feb 2, 2021 by a loss of 41 containers overboard off the M/V Aries operated by MSC shipping.
So what’s going on? Why does this appear to be happening with greater frequency?
Much of this is due to the push for ever larger vessels based on the theory of economies of scale. In less than 40 years, ships have gone from 5,000 containers back in the late 1980’s to 8,000+ in 2005 and now top 21,000 containers (TEU’s or Twenty Foot Equivalent Units). Todays leviathans carry more cargo in a voyage than the earliest generations carried in a year of voyages. With these economies of scale come some rather large problems to resolve.
The variables that factor in to any voyage plan would seem elementary, stowage departments have to factor in the weight of each container, the order of discharge based on the port rotation, the stack height and stack weight (you cant put too much weight in one stack or you crush the containers on the bottom), as well as the amount of weight that is going to disappear from the fuel oil burned off during the voyage which affects the ship’s stability. There are also a myriad of stowage rules for the various types of hazardous cargoes and where they can be stowed.
Before and during the early years of containerization, this choreographed ballet of applied physics and logistics was all done by hand. Today with 21,000 possible containers aboard, computers are supposed to calculate the most efficient stowage plan. However, stack weights are often exceeded and overweight cargo gets mis-stowed in an incorrect location. Vessels were at one time loaded for a “comfortable ride” not for the crew, but for the cargo. It is far better to load a vessel so that she will roll gently from side to side while underway. Put too much heavy stuff down low and you get snap rolling where the ships, just as the term suggests, rolls rapidly from side to side. Once again, physics comes into play.
On the smaller and older vessels, the containers at the top of the stack have a much shorter arc and are subjected to much less acceleration and force than the behemoths of today. Incidentally, container construction although improved, is not vastly different than it was at its outset other than size. Containers go below deck in a set of parallel rails and stack up to the deck level where a hatch cover is employed. Another set of containers is then stacked on deck and these are secured with stacking cones, lashings, and turnbuckles. These lashings need to be tightened on each container stack to ensure no movement while underway. Think about the number of lashings to secure the thousands of containers on deck. Ensuring these lashings stay tight and are in good working order is the responsibility of the crew once the vessel leaves port. A nearly impossible task on these massive new vessels.
So this is where we seem to have a breakdown.
Ships by their very nature are designed to operate safely in the worst mother nature can throw at them. Hurricanes, cyclones, and typhoons never to be trifled with are not supposed to be the undoing of a good vessel and her crew. By weather reports, the first casualty on November 30th occurred in a Force 4 storm (Force 12 is a hurricane) so the ship should have ridden out the sea conditions if loaded and secured properly unless an anomalous rogue wave did this damage. Only the continuing investigation will reveal the root cause. But for the others, it would appear that changes need to be made in how these vessels operate, the cargo they carry, and what vessel insurers are willing to risk when the stakes are so high.
Unfortunately, these casualties come with a significant cost and disruption for those companies that have cargo aboard waiting for a resolution. Resolution of cargo on some of these ship casualties may take more than a year so any product lost at sea and any product not lost but stuck in the legal morass now must be remanufactured. This forces customers waiting for their product from suppliers to push back their lead times as they wait for replacements. Safety stock or inventory buffers are an important concept to secure a resilient supply chain so when casualties like these occur, it minimizes the impact on an organization.